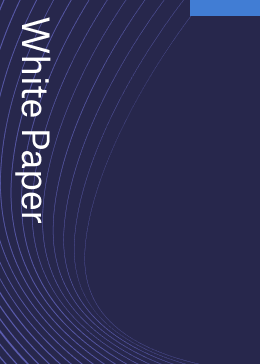
Foodservice Plant Cuts Costs and Equipment Downtime while Increasing Productivity by 80%
By Cold Jet
The General Mills Bakeries and Foodservice Plant in Chanhassen, Minnesota, is a leading producer of baked and unbaked food products. The facility produces a variety of goods, including flour mixes, doughs, bread, cake and cereal. After the goods are baked and ready for packaging, they are transported through cooling tunnels, which maintain the quality of the products while they are being transferred to the packaging area. With the high production levels of the plant, grease, oil, dust and flour quickly begin to accumulate on the conveyors, motors and panels in the cooling tunnels. The facility had been cleaning the tunnels with steam, water, and in some areas, by hand.
Given the highly regulated nature of food facilities, the cleaning method and process must be carefully considered by each plant.
The Chanhassen plant’s cleaning process was slow, inefficient and ineffective. The cleaning methods did not fully remove the grease, flour and other contaminants from the various surfaces of the tunnels. Machines within the cooling tunnels had to be shut down while a team of three workers cleaned the tunnels and collected the resulting wastewater.
Please download this free white paper to read more.
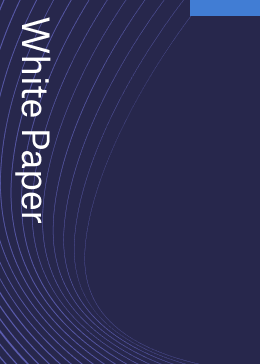