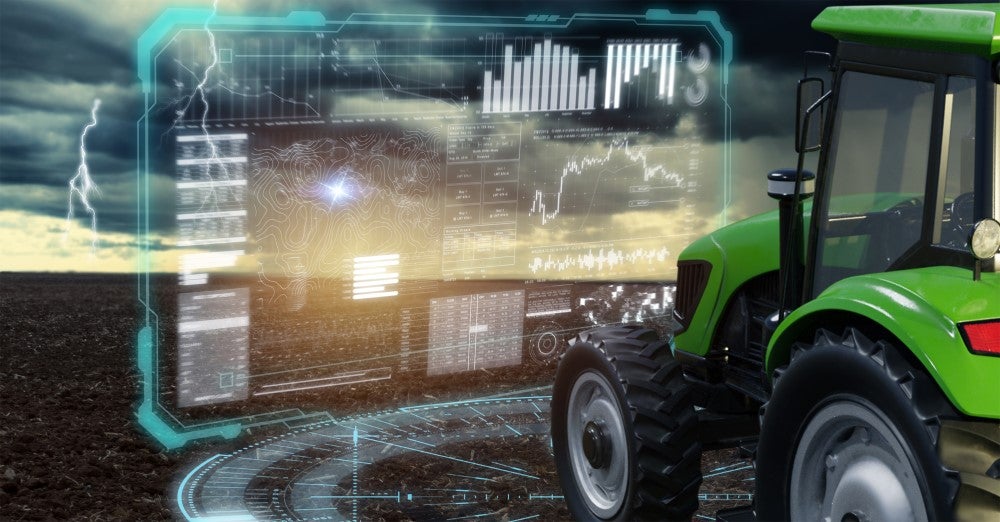
Blockages in the particulate filters require manual external cleaning – often resulting in expensive downtime. In light of changing market demands, Chevron has developed Texaco Delo 600 ADF.
This new oil is formulated with approximately 60% fewer of the metallic components contained in many conventional high-performance engine oils. Its new lubricant technology can extend cleaning intervals by a factor of up to 2.5 and reduce fuel consumption by up to 3% over the filter life.
Stricter emission regulations to reduce nitrogen oxides (NOx), particulate matter (PM), and other pollutants have driven the use of exhaust aftertreatment systems such as Exhaust Gas Recirculation (EGR), Selective Catalytic Reduction (SCR) and Diesel Particulate Filters (DPFs).
In 1999, Stage I European standards for engines used in Non-Road Mobile Machinery (NRMM) were implemented, and over the years, requirements for NOx and particulates have become more stringent, helping equipment become far cleaner.
Whilst Stage III and Stage IV led to limited use of DPFs, Stage V is driving widespread adoption of DPFs, which can be very effective at reducing PM emissions but require periodic cleaning to remove incombustible materials that accumulate over time.
Exhaust Gas Aftertreatment of Heavy-duty Engines
Unlike passenger cars, however, operating and maintenance costs are dominant in commercial vehicles and work machines. Due to their very long operating times, additional costs associated with exhaust gas aftertreatment must also be considered.
In a 2020 United Kingdom survey commissioned by Texaco Lubricants, 67% of respondents reported issues with emission control systems, including many that specifically referenced the DPF.
In fact, nearly half of the survey respondents indicated that they needed to force a manual regeneration of the DPF to restore its operation in service – an unplanned maintenance activity that keeps the truck off the road and out of service, and that also requires the burning of fuel.
DPF blockages that required cleaning or replacement were the most commonly reported issues.
The main reason for these problems is ash that results from metallic lubricant additives and remains in the DPF. The DPF collects up to 98% of particulate matter emissions in the form of soot and ash, the majority of which is burnt off during typical DPF regeneration cycles.
Unlike soot particles, however, the ash element is incombustible material derived primarily from metallic lubricant additives, that over time clog the DPF. Thus, manual external cleaning is required, resulting in expensive downtime. In addition, if too much soot and ash build up, the large amount of heat produced upon regeneration can result in DPF damage.
DPF clogging increases engine back pressure, and regeneration cycles, resulting in higher fuel consumption. This is because once the particulate filter reaches a sufficiently high operating temperature, it burns soot particles – a process known as passive regeneration.
If temperatures do not become high enough to allow continuous regeneration, active or manual regeneration takes place, in which the exhaust gas temperature is raised by injecting fuel into the exhaust to burn soot particles and unclog the DPF. This comes at a cost, not only the upfront cost associated with these devices and the numerous sensors and dosing units that enable them, but also ongoing operational and maintenance costs.
Additionally, clogged particulate filters can have a significant impact on productivity. In some cases, the engine will enter a reduced power mode until active regeneration is complete, resulting in unscheduled downtime. If too much soot and ash build up, the large amount of heat generated during regeneration can cause filter damage – resulting in a cost-intensive DPF replacement and downtime.
DPF regeneration can only remove the soot. The ash remains and ultimately determines the filter life. Machine owners are forced to remove affected equipment from service and clean the DPF – usually externally – resulting in further costly maintenance and downtime.
New “OMNIMAX™” Oil Formulation
Chevron has developed a new engine oil that helps solve this problem by containing around 60% fewer metallic components than many conventional high-performance oils. Texaco Delo 600 ADF, with OMNIMAX™, a Chevron-patented technology, is the first heavy-duty engine oil with the capability to reduce ash build-up in DPF filters, helping deliver system protection to both the engine and the emissions system.
Suitable for both on- and off-highway application, the lubricant is formulated with only 0.4 % sulphated ash – far lower than the American Petroleum Institute (API) and The European Automobile Manufacturers’ Association (ACEA) limit of 1 % sulphated ash, as found in most current heavy-duty engine oils. Even so-called “low-ash” engine oils can cause high ash loading of the DPF over time.
This also happens with Texaco Delo 600 ADF, but more slowly, as it contains 60 % less ash-forming additives. In addition, the ash resulting from the lubricant has a higher density in the DPF. Therefore, a higher active filter volume remains over the lifetime of the DPF.
During the development of the new oil formulation, the biggest challenge was to reduce ash without affecting the oil’s performance. By rebalancing the additive system and introducing new, lower ash-containing components, Texaco has developed a new technology for diesel engine oils. This required an entirely new formulation approach and extensive re-balancing of all components to help deliver the protection needed in the engine and exhaust aftertreatment system.
Test Procedure for Evaluating the New Engine Oil
Industry-standard wear tests that are part of the API and ACEA standards, in Original Equipment Manufacturer (OEM) testing and also field testing in actual in-use fleets showed strong wear protection. Tests with operators showed that by reducing 60% of the ash from the oil, you find 60% less ash in the particulate filter.
In the course of the project, however, other customer benefits became clear: fuel costs are often the most important operating cost of a fleet, but it is often unknown that the condition of the exhaust aftertreatment systems has a significant impact on fuel consumption.
In order to quantify the impact of ash quantity on fuel consumption, and to understand how it affects exhaust backpressure and DPF regeneration, Texaco Delo 600 ADF was put to the test in a systematic engine test. In controlled tests on the engine test bench, the DPF load under identical conditions was simulated and Texaco Delo 600 ADF was compared with a conventional oil with 1% ash.
At identical loads and operating times, the system with Texaco Delo 600 ADF had a significantly lower ash content. The study also evaluated how the amount of ash affected the exhaust backpressure that the DPF exerts on the engine. Since ash combines with soot in the exhaust, there can be a significant increase in exhaust backpressure.
For the same operating time, the DPF on an engine with Texaco Delo 600 ADF resulted in almost no increase in exhaust backpressure – not only because of the lower ash content but also because of the higher density of the ash, which allows for a larger active filter volume. Further tests showed that operation with conventional 1% ash oil resulted in up to three times more frequent DPF regeneration than with Texaco Delo 600 ADF.
The increase in fuel consumption when the DPF is fully loaded is significant. In the World Harmonized Transient Cycle (WHTC) test, the engine burned almost 6% more fuel when the DPF reached its total useful life (on 40 g/L ash load) compared to a new and clean system.
In comparison, the DPF of an engine operated with Texaco Delo 600 ADF over the same period showed only a 1% increase in fuel consumption. Averaged over the DPF usage interval, this means a fuel saving of up to 2.3%. This saving can be achieved in addition to the reduction in fuel consumption due to reduced exhaust backpressure.
Extended Oil Life and Increased Component Protection
Increasing oil change intervals has remained a trend in the automotive and work machine industries. Many OEMs have therefore included oxidation control as a key criterion in their specifications. Volvo, for example, has introduced the T-13 engine test as part of the API CK-4 standard and their own VDS-4.5 specification.
This is a very demanding test where the oil is subjected to an aggressive duty cycle with high operating temperatures and a reduced oil volume. The Volvo T-13 test will also be part of future ACEA specifications. Oils that meet Volvo T-13 test requirements must survive 360 hours of operation without significant oxidation or oil thickening.
Texaco Delo 600 ADF completed a Volvo T-13 test with double length of 720 hours before the limits were exceeded. Additionally, Texaco Delo 600 ADF meets or exceeds ACEA E6, E9, and a number of OEM specifications, and has demonstrated oxidation stability in industry, OEM, and field tests, providing the opportunity to extend engine oil drain intervals.
It has also been formulated to deliver valve-train wear protection and piston deposit control performance. The greatest advantages associated with Texaco Delo 600 ADF can be achieved in heavy-duty diesel engines with DPFs. Older equipment retrofitted with a DPF would still see the benefits of DPF life extension as well as increased fuel efficiency.
Conclusion and Outlook
The Texaco Delo 600 ADF, with OMNIMAX™ product line together with its additive technology can help reduce the rate of DPF clogging, resulting in extended DPF service life and less frequent DPF regeneration cycles.
Tests with a number of heavy-duty diesel engines have shown that cleaning intervals could be extended by a factor of up to 2.5, and fuel consumption reduced by up to 3% over the filter life.
Considering that fuel costs typically account for about 25% of the total cost of ownership of a commercial vehicle fleet, the fuel savings from Texaco Delo 600 ADF can provide a reduction in overall costs and increase a fleet’s competitiveness.
Major engine builders around the globe are looking hard at how they will meet the pollutant and greenhouse gas emission standards that will continue to phase in over the next seven to 10 years, while also continuing to meet customer demands.
Ultra-low ash oils like Texaco Delo 600 ADF will be instrumental to meeting the requirements of future products while offering engine builders the flexibility to help optimize their systems in terms of the space that emission control components occupy in the equipment as well as their up-front cost.
No doubt, the future is bright for this technology.