
Singapore has given the all-clear for meat created in a laboratory to be sold in the market.
The south-east Asian city-state’s regulator, the Singapore Food Agency (SFA), has given its seal of approval for cultivated meat products made by US firm Eat Just.
It is believed to be the world’s first regulatory approval for cell-based meat.
The Good Food Institute (GFI), the US non-profit that advocates for plant-based alternatives to meat, dairy and eggs, described the move as “an enormous advance.”
GFI executive director Bruce Friedrich said: “Singapore has thrown down the gauntlet and other countries need to pick it up.”
The organisation’s associate director of regulatory affairs, Elizabeth Derbes, said it is “confident that the SFA’s safety standards for these ground-breaking foods have been carefully calibrated to ensure consumer safety”.
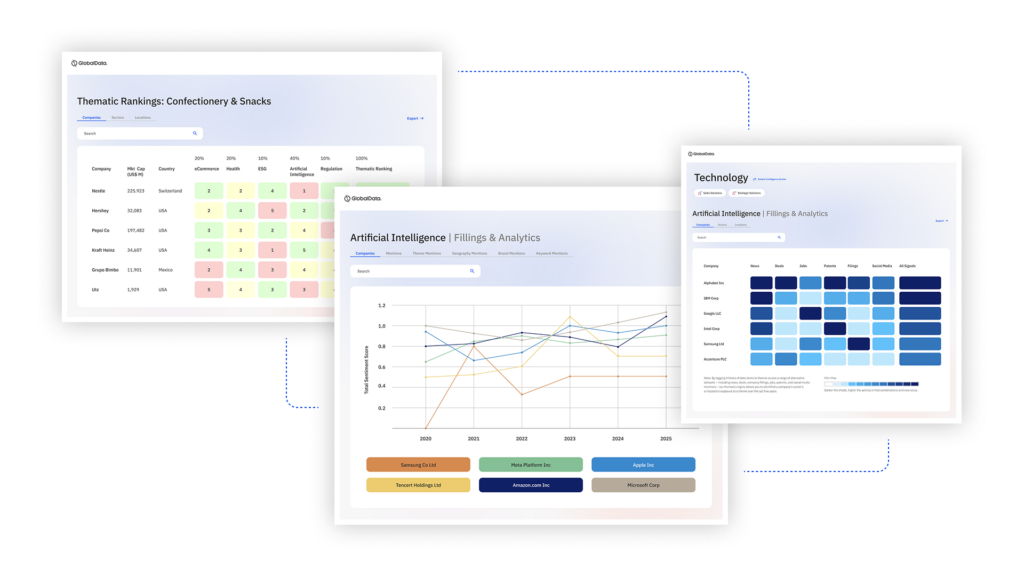
US Tariffs are shifting - will you react or anticipate?
Don’t let policy changes catch you off guard. Stay proactive with real-time data and expert analysis.
By GlobalDataEat Just is best known for its faux egg product. The company’s “chicken bites” which have been approved for sale in Singapore, initially in a local restaurant.
The cells for its product are grown in a 1,200-litre bioreactor and then combined with plant-based ingredients.
Eat Just founder Josh Tetrick said on Twitter he is “proud to share that Eat Just is the first company in history to receive approval to sell cultured meat (safe meat from animal cells instead of slaughtered animals)”.
Simon Powell, an equity strategist at US investment bank Jefferies, said Singapore’s approval of the cultivated chicken product “is evidence that disruption of the traditional meat industry is progressing as predicted”.
He added: “Cultivated meat grown in bioreactors still lags behind plant based meats but is set to emerge as a commercial alternative. As alt-protein moves from the laboratory to industrial-scale production, costs will reduce, potentially towards or even below conventional meats. Disruption is in play.”
Powell acknowledged the cost of cell-based protein remains higher than conventional meat but suggested there could be equivalence in ten years.
“There is significant runway for costs to reduce to the same or even lower than conventional meat,” Powell said. “Currently, the culture medium costs in excess of US$400 per litre and we estimate that to grow 1kg of meat in the lab could require 500-1,000 litres, hence the high cost of meat that has been grown so far. To scale up to a batch process that can produce 2,000 to 5,000kg of meat at a time will require bioreactors as large as 20,000 litres.
“In order to deliver the step reduction in the cost of production, the industry will need to significantly cut the cost of the substrate culture that the cells grow in. The trajectory of cost reduction taking place suggests that this technology could reach price parity with conventional protein in the next decade.”