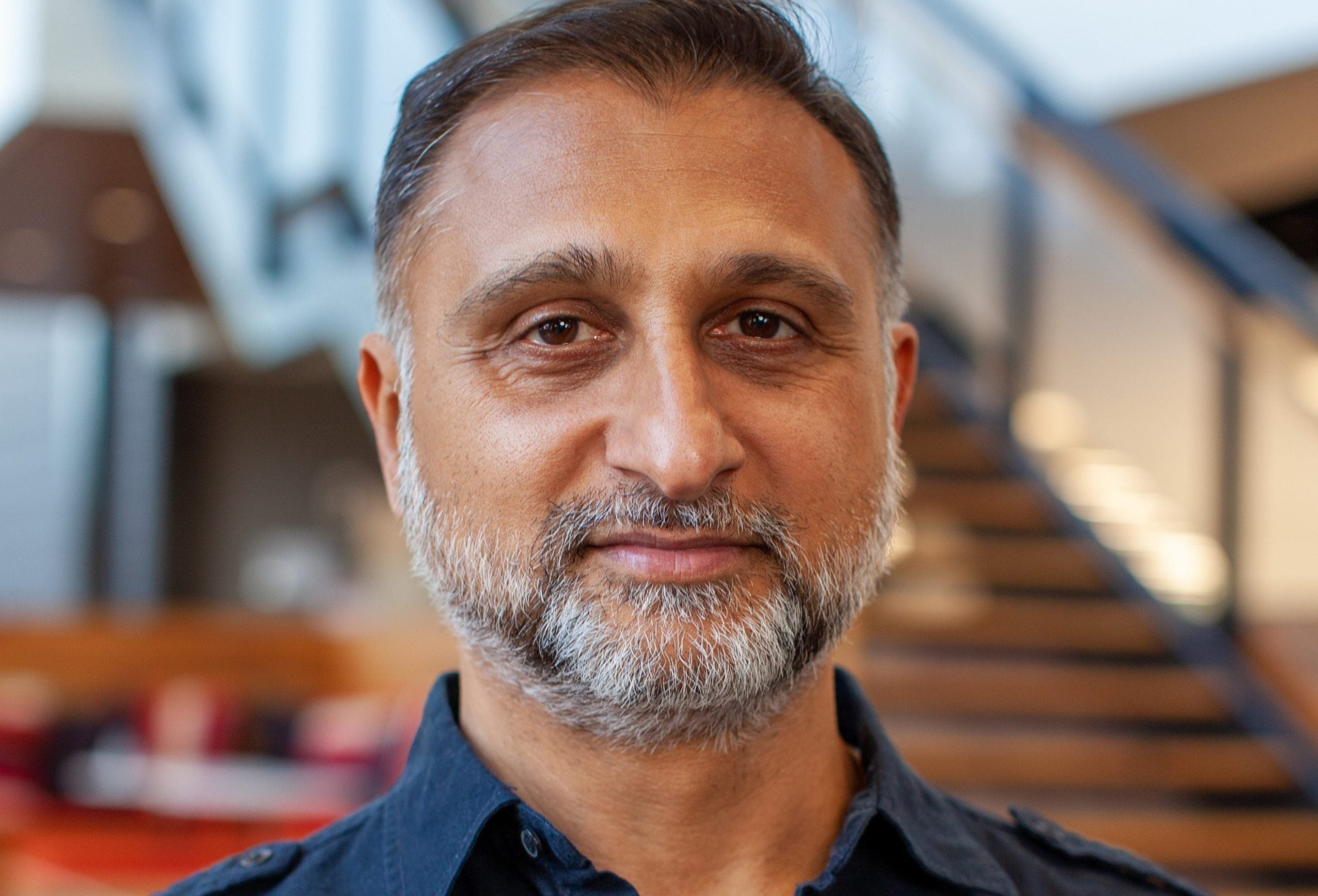
The world’s largest meat processors, already using tech in areas like packing, are investing in ways to make their production more automated.
One of the very biggest, Tyson Foods, has committed to investing more than US$1.3bn in adding more automation to its factories over the next three years.
Investment in automation is not new – two decades ago, Tyson was outlining to investors its spending programme in the area – but expenditure has accelerated in recent years as the pandemic and the ongoing pressure on recruitment has hit the pool of labour. Just Food sat down with Chetan Kapoor, head of optimisation and automation at Tyson, to discuss the US-based giant’s efforts.
Just Food: Given the amount of money Tyson Foods is investing in automation, what do you see as the principal benefits of the technology?
Chetan Kapoor: Team member safety is our primary driver for automation. Food processing plants are wet, they can be cold and there are sharp objects. Removing the exposure to them is one thing that automation does really well. Another is productivity. Automation added appropriately improves the productivity of our team members.
Third is food safety. Automation, machinery in general, has less variation and a more controlled environment should allow us to improve food safety. The fourth, which is much more longer term, technology in our plants allows us to upskill our team members. To use technology, you generally have a higher pay grade to do that, so as we transition to a more modern workforce, technology allows us to pay more. Of course, the number of people who work in our plants is going to go down with technology but we have enough attrition anyways for us to make that possible.
JF: That’s always the elephant in the room with technology. When Tyson Foods set out its $1bn automation investment, it detailed its labour requirement would fall by 3,150 positions by 2024. The company is, however, seeking to emphasise this is an opportunity for staff to become upskilled?
CK: That’s right. Also, we are a company on a growth trajectory. Even though we’re reducing people, we’re also growing at the same time, right? And so, with our number of headcount, as a percentage of revenue, yes, it should go down and we want it to go down but a level that is increasing overall. And we are in places where it’s almost impossible to hire people, that are in remote areas. We have a big challenge in staffing our plants.
JF: Has the pandemic and the related challenges around labour sped up investment in automation?
CK: Definitely, the pandemic highlighted dependency that we realised could be very challenging for our business and it did bring urgency.
JF: How would you describe the labour and recruitment pressures currently facing Tyson Foods?
CK: I know that some of the plants in poultry do have adequate labour but in some areas we don’t have adequate labour. The other aspect of labour is that there’s a significant turnover, which is also challenging.
JF: How specifically do you see automation helping Tyson Foods solve these issues in labour?
CK: On the beef side, for example, we’re very focused on taking out anything that is hazardous to humans. Bone saws are very typically used to cut big slabs of meat. Automating that fully with a robotics system, with computer vision is a top priority for us. We are already deploying them and, in fact, we had to invent our own machine because we could not buy machines on the commercial market that would fit into our process.
Then we are finding there are certain jobs, like de-boning chicken and some of the cuts that a human has to make, are extremely taxing on the fingers. Automating that through robotics is a high priority. The challenge there is you want to do it with the precision of a human, too, not just the dexterity of the human. That makes it technically really difficult but, again, Tyson has invested in its own R&D to solve those problems.
Another area we are looking at is non-value-added tasks where you’re just doing material movement, transferring something from here to there. Those things if you add up take a lot of labour. They are also highly repetitive and tasks prone to injury. Automating that is a big part of it and that’s actually a relatively easier part technically, because it’s being done in other industries.
Productivity in our plants is more than automation. Automation is trying to alleviate labour challenges through machinery. Another part of it is digital technology we are deploying in our plants under the ‘smart factory’ initiative that improve the productivity and the efficiency of the capital that we have invested in our team members, in our equipment and in our infrastructure. Tyson makes all our money in our planks. That’s where we live and die. Most of our capital is in buildings, equipment and team members. How do I get the maximum productivity out of these?
We have a major initiative, a ‘smart factory’ initiative, to deploy technologies that drive productivity in these areas. How do we improve team member engagement and problem-solving through technology? How do we get more visibility into the equipment in our plants? Where are the bottlenecks? Why is there downtime? Why is one machine working really well in one plant and not delivering in another plant when it’s the same machine? We have so much scale that we can learn within Tyson itself to optimise our operations.
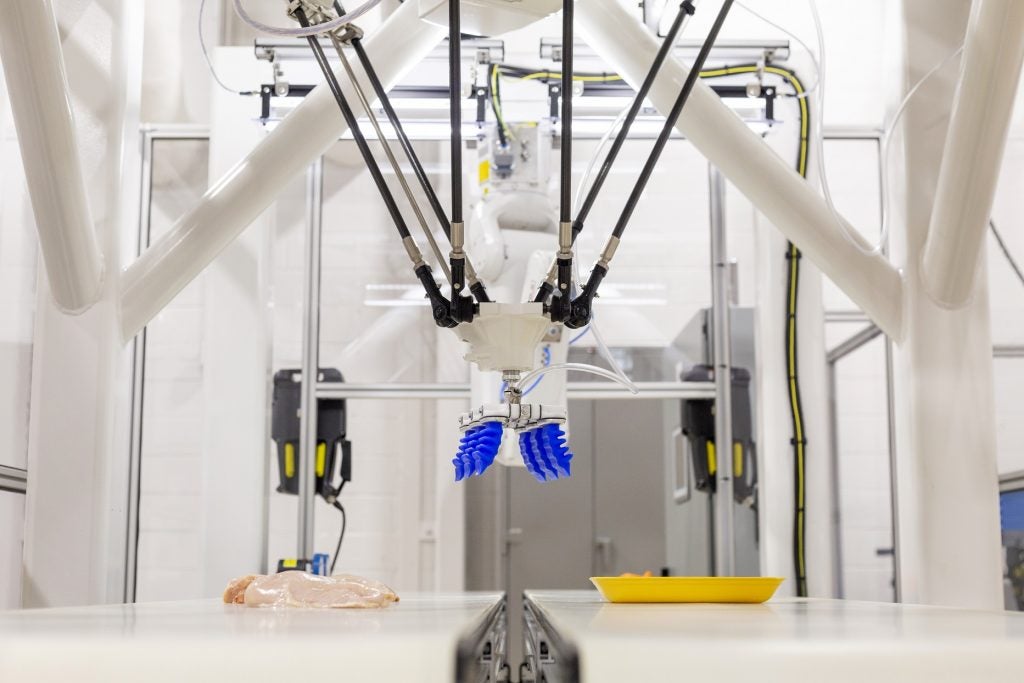
JF: The repetitive tasks you sketched out. Are there still areas of opportunity for Tyson Foods to go after?
CK: It’s stacking boxes. It’s putting product into a box itself. It’s also putting protein into trays. When you go to a store and buy a tray of chicken or pork, somebody had to put it in that tray. It’s likely a human who did that. Today, robotics with computer vision can do the same thing and do it at speeds at times exceeding humans. We are actually deploying those technologies.
JF: However, the examples you gave on sawing beef and on de-boning chicken, are they at an earlier stage of deployment?
CK: That’s right. We are saying instead of picking the most difficult things to automate, pick the more obvious, the easier things to automate but invest in things that are unique and specific to Tyson for the long term that sets us competitively ahead of everybody else.
JF: What parts of the ‘smart factory’ initiative are you most excited about?
CK: The biggest benefit is a lot more engagement from team members, alongside the technical people in the plant and the management of the plant to solve problems as they show up and to get visibility into where the problem is versus stories and anecdotes. Data-driven, more collaborative, problem solving, a little bit more of an agile approach to running our plants and distilling the data then to higher level decisions within the company.
So think of it like a line supervisor looking at the line, the plant manager is looking across a plant [but] the complex manager is looking across multiple plants and the VP is even further ahead. Right there, they’re able to compare and contrast, make decisions at the right level of data that they need. This is a big opportunity.
JF: As well as being a big opportunity, has there had to be a big job of education within the plants for some of the staff still working at Tyson Foods who may fear for their own jobs?
CK: With this kind of technology, it’s not a job question because you’re improving the productivity and getting out of our plants what the plants are designed for. Generally, you would put these technologies into a plant that is not performing to the spec they’re designed for. So, you may have to overspend on labour by going overtime, or you will be spending a lot more on equipment maintenance than you should be. It’s more of an efficiency gain versus a headcount challenge over here.
JF: What about the tech for workers currently in packing or in the processing of the meat? How has Tyson Foods sought to discuss with them the increasing use of automation within the plants?
CK: I’m going to answer based on anecdotes. You take somebody to automation and invariably somebody is nervous. There’s no denying that but then they find out that there’s 30 different openings and 20 new hires every week, so they also look at that reality, right? You’re hiring, continuously hiring.
I’ve also seen team members get excited about automation. We put one piece of automation in a plant local over here, a box stacking robot. One person who was originally stacking boxes, he was nervous. Then the plant manager spoke to him and said ‘Hey, you’re not going to just be doing this.’
There was another lady, a 60-year-old Hispanic lady who came and said ‘I’m going learn how to use this robot.’ Now, this robot was beautifully designed to be very friendly and had an amazing user interface to make it very easy for our team members. This lady came and actually muscled her way in, she took after it and she was operating the machine. She called it her first computer. She couldn’t speak English, the user interface had French on it but we translated it into Spanish. And then, because of her excitement, her family bought her a computer. So there’s that story. For every person who feels some anxiety about it, there’s plenty of opportunity within Tyson, there’s more people feeling hopeful for a career that is more fulfilling.
JF: What about the concern increased digitisation could increase potential vulnerabilities to cyber breaches?
CK: Anything I do, I got three boards that I have to clear and one of them is a security board – and you can imagine how much fun that is. They are extremely diligent and restrictive. We have multiple layers of security and networks that you can’t even get to from outside. They’re segregated, sliced and diced. Every software that comes into our plant with new machines has to go through a standards approval process. We have very strict standards on what kind of computer they can have, what kind of operating system they can have and it’s really all done to mitigate the risk of potential breach.
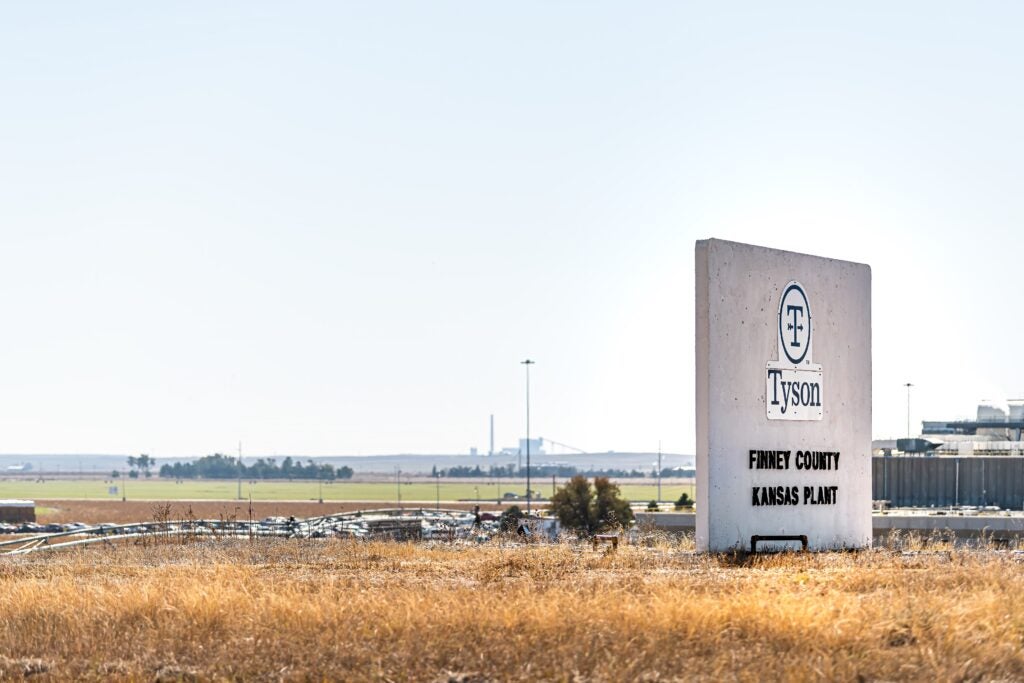
JF: When you look to deploy certain technologies, how do you look to mitigate that risk?
CK: Tyson is extremely concerned about this, just like any other major, Fortune 100 company should be. We have enough processes in place to make sure that some of these things don’t happen – and then there are processes in place to [see], if something were to happen, how do you immediately quarantine it?
JF: Looking at Tyson Foods’ international footprint, how much do you share the deployment of technologies like automation across your different geographies?
CK: A lot of the plants that Tyson has overseas came through acquisition. They all have different levels of automation. We have a plant in Thailand that is very nicely automated, runs beautifully. Right now, we are less focused on the international than we are on the US. A lot of it is because of labour availability wherever it is.
JF: For now, then, the US remains the priority.
CK: We are actually looking at all of them and all the standard solutions that we are coming up with are being shared and some are being deployed in Asia. Is it a 100% push yet? No. On the other front, I talk about automation and then I talk about digital? The smart factory thing we’re doing here in Tyson [in the US], we’ve actually already done it in our international business. On that front, they are leading ahead of what we’re doing in the US.
JF: Can you share any examples?
CK: We recently did a productivity tool in equipment monitoring deployment in all our plants in Asia, 15 plants. It was done very well, it showed great results and that’s what prepared for it to come back through here. It’s almost like some of the international locations are much more entrepreneurial, to try new things.
In my previous job, I used to work in a Japanese company and we did a lot of business in China, too. I had a start-up in China also and I found in the automation and factory space, you were able to hire highly skilled engineers in Asia more easily than you can in the US. So, when you approached plants in Asia with new technologies that could improve efficiency, the uptake from them over there was much higher and quicker. They have good engineers who came from good schools readily over there, versus in the US, based upon where plants are located.
Manufacturing in general has never been at the top of the game over here [in the US]. There’s been more software technology. The talent pool definitely was gravitating higher on that side. More innovative approaches, more adoption of tech was easier [in Asia]. And less risk, right? Smaller operations over there.
JF: How can the US increase that pool of engineering talent domestically? Does that need government support?
CK: Well, the US government and different institutions are doing it enough. Companies have to make a concerted effort to make an investment in that area themselves, just like Tyson is doing with its various programmes to upskill its team members. But as long as you are also innovating on the software side of things to do, where the US has kind of led the world, there’s always going to be that challenge. When companies in Silicon Valley can take most of your talent and pay them a dramatically higher amount, it’s going to be challenging. This has changed in the last six months with the tech sector going a little bit slower. We have a lot more people starting to approach us. Things are changing in a direction we like.
JF: Are there newer, more emerging technologies that Tyson Foods is looking to use in your automation and digitisation?
CK: Yes, we are. Just measuring the amount of meat left on a carcass using computer vision, that’s an area we’re looking at very dramatically. There’s some other areas that I don’t want to necessarily talk about but that have a significant AI and machine learning component. There’s no other two ways to do it.
And then there’s also optimisation across the enterprise. As humans, we’re good at doing local optimisation. We can kind of manage it. Looking across a very complex organisation, with so many business units and the bazillion amount of SKUs we make and a very highly integrated supply chain, how do you optimise that? This is not a software problem. This is not an algorithm problem. This is an AI problem. So, there are things over there that are very, very promising that we are looking at and actually doing.
JF: And feeding right the way back to Tyson Foods’ overall fiduciary duty, this work has a direct impact on your revenue and profitability. That’s the whole point, isn’t it?
CK: It has to.