Recent food scares have put traceability and crisis management at the top of the agenda for food processors. Modern technology can achieve a great deal in forwards-and-backwards traceability and offer manufacturers a significant competitive advantage and genuine cost savings. Len Smith reports
Thanks to growing consumer pressure, traceability and crisis management are fast becoming two of the dominant issues facing retailers, food processors and suppliers today. All of which must be making the early prophets of enterprise quality management (EQM) feel smug. Certainly Donal Deasy, the man who invented the term and who arguably conceived the whole concept of EQM within the food sector, is suddenly in demand as a speaker on the international conference circle.
He sums up the problem rather nicely as the ‘basement syndrome’. ERP (enterprise resource planning) systems, he claims, have been remarkably successful in addressing the needs of the proverbial 12th and the 13th floors – such things as financial management and control, sales order processing, stock control and, possibly, customer relationship management. They have also addressed many of the needs of the 14th floor – executive information systems and business intelligence. Where they become flaky is further down the organisation and none has really succeeded in addressing the basement where murky activities like quality control, quality management, process control, laboratory information systems, and so on, operate in splendid isolation.
His own company, now known as Qualtrace Solutions, has over the years developed quality control and process manufacturing software solutions – all aimed at putting quality at the centre of enterprise systems. It was some time around 1992 that Deasy cultivated his vision of ‘bridging the traceability gap’ between process automation and business systems to improve the rapid response and crisis management capabilities of food processors. Ultimately, this was to be achieved through better data capture, real-time access to and validation of data, and improved systems integration. New technologies have made this eminently possible and, if recent Qualtrace implementations are typical, payback periods are incredibly short.
“It’s a carrot and stick scenario,” according to Deasy. “The potential costs of a food scare are horrendous. Snow Brand, Japan’s biggest dairy producer, provided a painful example when it lost US$91.5m between April and July 2000 following an outbreak of food poisoning that affected 13,000 customers. Unable to identify the contaminated batches accurately or quickly, Snow Brand was forced to withdraw all of its products from retailers’ shelves and shut down 21 plants for 40 days. The carrot is the up-front savings from improved productivity plus added value along the supply chain. We are currently involved in a major implementation with a payback period that has been assessed independently as less than 12 months.
“The secret is not to see quality and traceability as a compliance issue but as an integral part of the whole manufacturing process” |
The example quoted by Deasy is United Milk‘s pioneering plant in the UK, which is particularly illuminating in that the dairy industry suffers all the problems of other food sectors and some more besides.
How well do you really know your competitors?
Access the most comprehensive Company Profiles on the market, powered by GlobalData. Save hours of research. Gain competitive edge.
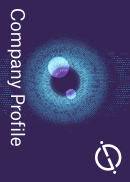
Thank you!
Your download email will arrive shortly
Not ready to buy yet? Download a free sample
We are confident about the unique quality of our Company Profiles. However, we want you to make the most beneficial decision for your business, so we offer a free sample that you can download by submitting the below form
By GlobalDataUnited Milk is a recently formed farmers’ cooperative whose new £45m (US$63.3m) plant will process 850 million litres of milk a year (nearly 6% of UK milk production). Its objectives:
- To be the most efficient milk processing plant in Europe
- To achieve full forward and backward traceability for product and plant equipment – from cattle feed to milk powder, from collection tanker to bagging
- To provide internet integration for farmers, suppliers and customers
- To achieve minimal environmental load
The plant needs to be efficient – it offers dairy farmers, its investing shareholders, 1.3 pence (US$0.18) per litre above the intervention price. This is particularly relevant in a business environment where competing processors have traditionally driven raw milk prices down (the UK dairy industry has no real history of vertical integration) and the end products are experiencing flat demand. The company’s competitive advantage, in a commodity market, is that it will offer customers complete product traceability. The United Milk plant has been specifically designed to ensure optimum traceability in all areas. The
“Consumer/retailer campaigns against GM food and media interest in food scares means the multiples are beginning to recognise traceability as a way to build consumer confidence” |
Of course, future benefits may be easier to describe than to achieve but the level of external investment that United has attracted is a measure of confidence. Don Morris, UM’s CEO sums up “We’re very confident of success. What we are doing is bringing together a number of best-of-breed solutions and practices. Where we have been particularly innovative is in the degree of integration.
Overseeing the project is a closely knit working group that includes our own internal specialists, an external independent consultant and a lead contractor and communications along the supplier/contractor chain are excellent. The whole project has been thoroughly researched and is controlled using the tightest possible project management methodologies. As a farmers’ cooperative we have a group of very willing suppliers who recognise the competitive advantage that traceability can offer. We appreciate Qualtrace’s industry knowledge and focus on enterprise quality management, of which traceability is just a part.”
Payback period under one year
This outlook has been confirmed by an independent White Paper, published in June 2001 by the ARC Advisory Group, an international leader in providing strategic planning and technology assessment services. In its assessment, United Milk will succeed because of the “unique business advantages” of systems integration between automation and enterprise business systems. ARC compares the traditional view that traceability is just a regulatory requirement with United Milk#;s ability to “differentiate a commodity product, maximise sales value of batches by identifying the exact grade specified by customers and… automating routine record keeping”. The report goes on to comment on United Milk’s capacity for crisis management. As to return on investment, ARC sums up “The IT systems and the associated integration will cost around £2m (US$2.8m). ARC estimates the payback period on the cost saving that United Milk achieves from the IT systems integration, the traceability and the plant maintenance system at under one year”.
United Milk, of course, has the advantage of being a ‘green field’ development. Most food processors have significant investment in existing plant, legacy computer systems and possibly mixed hardware platforms. According to Nick Ford, Qualtrace’s Country Manager GB, this is no real impediment “Although some of the benefits of UM’s automation may be difficult to introduce into an existing plant, the traceability and quality management aspects can be achieved with some minor physical and operational changes. The concept isn’t restricted to the dairy industry or large processors. We have a range of quality and traceability implementations in operations of all sizes – companies ranging from Newmarket Cooperative, a small Cork-based cheese processor, to Bantry Bay Seafoods, a leading seafood processor, to IAWS, Scottish Milk, Glanbia and FMC BioPolymer.”
So, how could it all work in an existing facility? “You have to remember that most plants suffer from non-integrated applications from different disciplinary areas and integration has always been a huge issue in the IT industry,” says Ford. “That’s why we have specialised in addressing the integration issues for some years. An electronic data chain can provide levels of traceability that are impossible to achieve with paper systems or electronic data islands that use paper to bridge the gaps. The critical components of electronic traceability are the combination of a laboratory information management system (LIMS) with the physical tracking of material and equipment, and the full integration of laboratory data with all operational areas. These are the very areas we have made our speciality.”
Ford keeps returning to Deasy’s concept of the traceability information gap. “Most processors have a stand alone LIMS, which means manual keying of data, telephone communications between departments, and transcribing data into other systems – with all the opportunities for misunderstandings, human error and so on. The net result is duplication, errors and islands of information. When a plant has a quality audit, or a real food safety problem, an army of people has to search physical archives, laboriously negotiating a paper document-chain for the information necessary to manage the crisis and minimise the damage. During the time this takes, the client#;s confidence is dipping fast. Once you put quality management systems at the centre of the IT systems, on an equal footing with say the financial systems, fully integrated into each stage of the process, then you have an electronic solution to forward-and-backwards traceability in minutes. It really requires a management culture change.”
Change in management culture
That change in culture has begun and it is not restricted to the food sector. Where conventional wisdom used to dictate that ERP solutions had, by definition, to come from a single supplier, today companies recognise the value of adopting best of breed solutions for highly specialised requirements, provided they can be integrated within the overall IT infrastructure. Similarly, those perfectly sound legacy back-office systems or in-house developed solutions are ready to adopt an integrated add-on offering. Interestingly, this new philosophy is being welcomed by leading ERP solutions suppliers, who recognise the commercial advantage of co-operation with specialists – particularly those addressing Deasy’s ‘basement’ applications.
Only this month, Intentia, the e-collaboration solutions company, signed a strategic partnership agreement with Qualtrace Solutions. Intentia has built a large, global customer base in the food and beverage markets and according to John Gledhill, head of the company#;s food and beverage application centre, “This is an opportunity to cement that leadership by offering a fully integrated, collaborative solution for the supply chain that will directly address the traceability issue”.
“ It#;s in everyone#;s interests to share responsibility for putting pressure on governments to ensure we have common standards both across Europe and globally“ |
As to how long the culture change will take, Deasy believes that there is a definite window of opportunity for processors. “Five years from now, pressures from the multiples will mean that processors will have to demonstrate their ability to respond quickly in the event of a food or health issue. Multiples will insist on auditable enterprise quality management systems. The pressure will become irresistible and those companies that make the appropriate moves right now are the ones who will seize the competitive advantage. The others are just reserving a plot in the graveyard of businesses that failed to recognise the inevitable.”
By Len Smith

Qualtrace can be visited at www.qualtrace.com. Copies of the ARC White Paper can be obtained, free of charge, from Qualtrace by e-mailing eodriscoll@qualtrace.com.
To view related research reports, please follow the links below:- The 2000-2005 World Outlook for Food Processors |