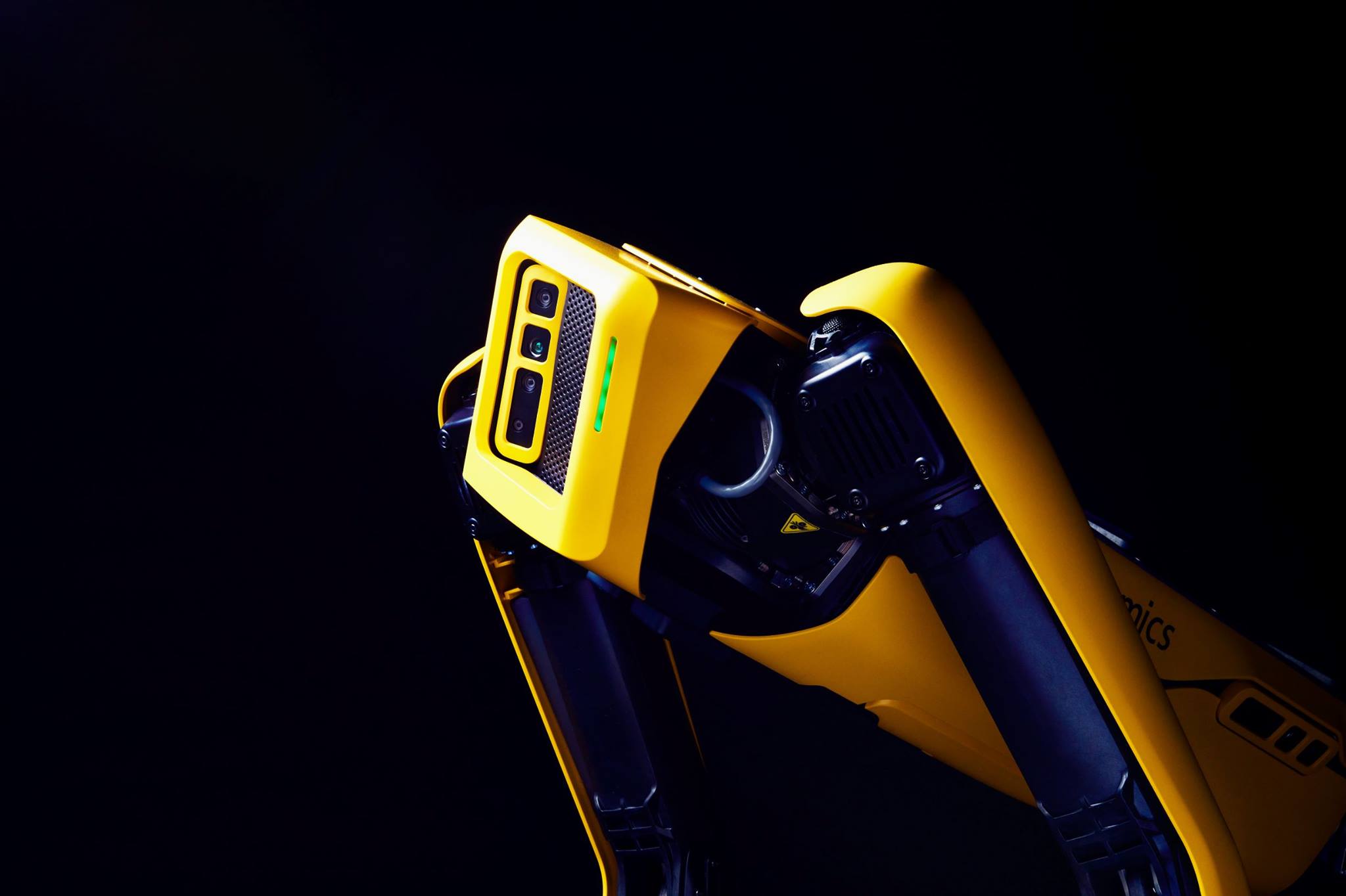
Spot is not your average factory worker. For starters there’s the unusual name and the fact Spot has four legs and is painted bright yellow.
While Spot may look out of place on a factory floor amid a sea of human factory workers, the ‘robot dog’ developed by US engineering group Boston Dynamics could play a vital role in ensuring food manufacturing plants function smoothly in the future.
Many of these factories are filled with large machines and conveyor belts churning out identikit versions of products minute after minute, day after day, until one day a machine or a belt breaks down and valuable downtime is lost while a repair is carried out.
In most cases before these machines fail, they show signs they’re about to fail. There might be a slight change in the vibration of the machine or the machine’s heat level might increase fractionally a few hours before it eventually breaks down.
So Spot is taking part in a predictive maintenance trial at an unnamed food company in the US. The robot dog has been fitted with sensors and programmed to walk around the factory floor to capture changes in the heat levels or vibrations that machines emit. The data is then fed into a piece of AI software that can determine if the variation is within or outside normal parameters. If the variation falls into the latter category, pre-emptive maintenance can be arranged before the machine breaks down.
The pilot has yielded promising results and it’s possible Spot could be rolled out in other food manufacturing sites to help reduce downtime and improve productivity levels.
The business benefits of AI
As the global food industry tries to get to grips with supply chain bottlenecks, soaring inflation, scarcity of materials and crippling labour shortages, the business case for investing in robotics and AI/machine learning like Spot has never been stronger.
Technology experts argue AI and machine learning can deliver efficiency and productivity improvements and cost savings to food manufacturers in all manner of different business areas, from supply chain management and logistics through to predictive analytics and NPD.
But how might food manufacturers’ investments in AI change how they staff their blue-collar and white-collar operations? Will the technology replace or complement human workers?
Nilpesh Patel, partner at OC&C Strategy Consultants, thinks “from a macro perspective” there is a significant opportunity for the increased use of AI and machine learning technology across the food and drink sector over the coming years”.
He adds: “Given the context many food and drink players are facing, with rising input costs, scarcity of some of those input materials and staff labour shortages, all of those things are a good environment for AI to drive efficiencies and help some of these companies solve some fairly medium- to long-term labour challenges.”
Patel says that, to date, the use of AI and machine learning by food companies has largely been in more customer-facing areas, such as predictive analytics and deciding what ranges to put in stores to drive rates of sale. The technology has also made its way into manufacturing processes where it has multiple uses including sorting products into different grades and identifying production anomalies.
Where the technology has struggled to make inroads so far at least is in areas like meat processing, which require a high level of skill and precision to cope with different processing variables.
“Obviously, every single chicken or pig that comes down the line is a different shape and a different size and so, while elements of meat processing are automated, there’s still quite a lot of human butchery and skill involved to get the best yield off the animal,” says Patel. “A combination of better robotics and better AI to make sure that the robot is cutting in the right place could drive further efficiencies in those places.”
It’s an opportunity Abhinav Agrawal, managing director for digital at management consultants AlixPartners, is looking to exploit at a meat processing plant for a client. To improve accuracy and reduce the need for the inspection of cuts of meat, which is a fairly manual operation historically undertaken by humans, the company has coupled a computer vision camera with AI to grade cuts coming off assembly lines.
“Within a week of training the AI algorithm it was able to determine if the cut was good quality or bad quality and, although it was not 100% [accurate], it was performing better than a human,” says Agrawal.
AI can complement humans, firms insist
There are numerous other potential applications of AI and machine learning in the food industry and several manufacturers have already invested significant sums of money in the technology as they seek to gain a competitive advantage over rivals.
However, because they are highly protective of their ‘secret sauce’, finding out specific details around how they’re deploying the technology is challenging – all of the large food groups contacted for this article declined to comment. And the fact that AI, machine learning and robotics could in some areas replace human workers makes it even more of a sensitive topic.
One community more willing to discuss the benefits AI/machine learning is giving their businesses are food start-ups, such as vertical-farming company Future Crops, which is just embarking on an AI trial at its site in The Hague. It intends to use the technology to monitor plant growth and stress to help fine-tune its processes and improve yields.
Gary Grinspan, CEO of Future Crops, says the company uses agronomists to make observations and corrections to its processes but it intends to deploy AI to perform a task that humans couldn’t possibly do.
“The amount of parameters you need to check [in relation to the plants] is too big and too wide and you can’t control everything,” says Grinspan. “Secondly, just think of a room in vertical farming, which is ten floors high. Every hour you need to be on every floor in every space of the room to see what’s happening with the plant, so you will need many, many, many people to do the work an AI machine learning tool will be able to do.”
It’s a similar story at US-based Vertical Harvest Farms, which also uses AI. However, as is the case at Future Crops, Vertical Harvest’s co-founder and CEO Nona Yehia, says the goal with its farms is to create jobs “not to automate them away”.
“The ways in which we’ll use technology like AI and IoT systems is to enhance our data collection to better understand how plants are growing and under what conditions,” says Yehia. “This way we can increase our yields per square foot and better use resources like water and energy to further our sustainability goals.
“In this respect, the IoT sensors throughout the farms can see and understand what’s going on with the plants at a level deeper and faster than the human eye or brain can perceive. This allows us to address any growing threats before they’ve visibly compromised at crop cycle and keep the farm operating at its best. We are not planning to use next generation technology to reduce jobs in the areas of seeding, harvesting and/or packaging like some of our CEA [controlled environment agriculture] competitors.”
Yehia adds Vertical Harvest’s new farms will create between 40 to 50 jobs at each location and her goal is to use technology that complements farming and doesn’t replace human farmers.
Animal-free dairy protein company Imagindairy shares this vision. Eyal Afergan, CEO and co-founder of Israel-based Imagindairy, says AI and machine learning are enabling the company to create an efficient microorganism that can produce large amounts of dairy proteins.
“This makes our fermentation process more efficient meaning lower production cost for our protein,” he explains.
“The AI we use is definitely complementary to the work done by Imagindairy’s employees. They are those who implement the recommendations from the machine learning engines and make them a reality in our labs. The combination of our team’s expertise and experience, alongside the AI technology, is our secret sauce.”
Another food start-up that sees AI and human workers working hand in hand as integral to its development is NotCo, a Chilean food-tech company producing plant-based alternatives to animal-based food products.
NotCo has developed a patented AI technology called ‘Giuseppe’, which uses a proprietary database of more than 300,000 plants and matches them at their molecular level to create a product that tastes, feels and functions just like its animal-based counterpart.
“Our scientists, culinary chefs, and engineers work together to develop and perfect Giuseppe,” says Matias Muchnick, CEO and co-founder of NotCo. “Each member of our team has their individual strengths and plays a unique role in our process of creating these alternatives that mimic the real thing.”
NotCo, which has attracted more than US$350m in investment, sells plant-based meat and dairy products in markets including Chile, Mexico and the US. In February, it announced a partnership with Kraft Heinz to launch products using AI.
The rise of ‘cobots’
The start-ups interviewed by Just Food have realised AI technology works best when it works in harmony with humans, whether these humans are experts in certain areas such as agronomists, or merely providers of physical labour. As a result, the fear that the growing use of robotics and AI/machine learning will one day lead to a scenario where human workers are no longer needed could, some say, prove well wide of the mark.
Fero Labs is a US-based business offering factory optimisation software that uses real-time production data and white-box machine learning technology to deliver live predictions and recommendations. Berk Birand, Fero Labs’ CEO, thinks blue- and white-collar workers could end up benefitting from greater adoption of AI by food companies.
“While many suspect widespread adoption of AI will cut down on hiring, we at Fero don’t think that’s necessarily the case,” Birand insists. “In fact, software like Fero can be a training tool that helps workers develop the necessary skills to get hired for more highly paid jobs. Software can also free up industrial data scientists from tedious tasks so they can spend their time solving real problems.”
AlixPartners’ Agrawal agrees that although the implementation of AI could lead to the replacement of some human workers the reduction in workforces won’t be as dramatic as many people fear and the likely scenario in the future will see collaborative robots – or ‘cobots’ – working with “humans and doing better things, because humans are good at some things and machines are good at some things, and when they’re working together, they’re much more effective”.
OC&C’s Patel also sees AI and machine learning technology increasingly becoming another tool in the arsenal of back office and central head office teams that will work in tandem with humans rather than replacing them. As for those manual jobs on farms or on factory floors where labour shortages are already a major issue for many food groups, he thinks AI and robotics could prove a godsend.
“In a world where all the jobs can’t be filled at the moment it would be a welcome reprieve to the industry, if there was something that could help relieve some of the burden of labour shortages,” says Patel.
So, while the sight of Spot wandering around a factory floor might seem like a scene taken from a dystopian science fiction film, in the future of food manufacturing robotic dogs working alongside humans could become an everyday reality.