The global economic downturn has exacerbated the cost pressure food manufacturers are facing, at the same as regulation has increased and scrutiny on the supply chain has intensified. In this month’s just-food management briefing, MJ Deschamps looks at Enterprise Resource Planning, software systems that aim to help companies manage cost and monitor their supply chains.
Food manufacturers, distributors and suppliers worldwide are looking to enterprise resource planning (ERP) computer systems to help streamline their businesses, and make the shift from using basic, disconnected food industry software. A holistic ERP system can replace multiple databases with a single, centralised data source, with information relating to products, services, customers and suppliers accessible by anyone in a company. These interconnected and robust systems can be powerful, integrating internal and external management information across an entire organisation.
The aims of ERP systems are ambitious: to enhance the ability of the food industry to operate safely, efficiently and effectively, minimising costs, while ensuring proper labelling, handling of raw ingredients and food safety. In short, food industry companies need to communicate and process information at full capacity, to meet demands.
The underlying principle in ERP systems, says Tom Pirko, president of US-based international food and beverage advisory firm Bevmark LLC, is that information makes a lot more sense if it is linked together and is framed in a relevant context. “The smarter a company is, the more productive it is,” he says. According to Pirko, it is essential for top-end, highly competitive food manufacturers to have access to as much information as possible – and as quickly as possible.
For companies of all shapes and sizes, though, he says, ERP systems are becoming increasingly valuable. Companies will be able to prosper (or not) based upon how well they understand and integrate each and every part of their business.
“We live in a world that is so drenched in information and data – and it is extremely usable – but not if you don’t have the applications, and the ERP systems to be able to take advantage of it,” Pirko says.
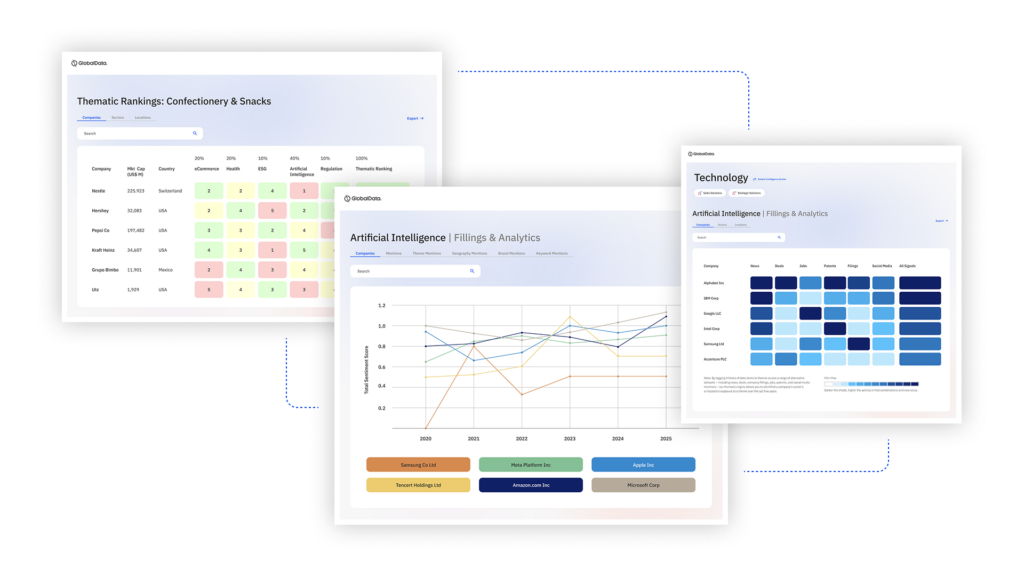
US Tariffs are shifting - will you react or anticipate?
Don’t let policy changes catch you off guard. Stay proactive with real-time data and expert analysis.
By GlobalDataAccording to Bob Swedroe, president and CEO at US-based Expandable Software, there are considerations and requirements specific to the food industry that ERP systems can help facilitate. These include compliance with local, national and international regulatory agencies with regards to mandatory production controls (for both normal manufacturing and quick responsiveness to situations where a tainted product is discovered); information and tracking of lot expiration dates; and monitoring supplier quality and on-time delivery performance.
Although they all work together in the same industry, ERP requirements for food manufacturers, distributors and retailers do differ slightly, Pirko says. “There is a much more engineered approach adapted for people who make the products and rely upon information, for example.”
James Wise from Canadian-British ERP software company Solarsoft Business Systems concedes his company primarily keeps food manufacturers in mind when developing ERP systems. “Manufacturers are kind of the heart of regulatory requirements – you have to track food as it comes in the door, gets processed and packaged and ready to ship. So we provide tighter controls around that aspect of the manufacturing process of the system,” he says.
The importance of a strong ERP system on the manufacturing end is essential for food distributors and retailers too: as they exist on the frontlines of the food industry, they can be quite demanding on manufacturers any time they receive a complaint, or gain knowledge of a food-related illness. “They can come down pretty hard and want answers virtually immediately from the manufacturer of whichever product is in question,” he says. “That’s truly what the ERP systems will provide to [manufacturers] – the ability to respond quickly to an inquiry that will keep their business whole.”
Some additional benefits of ERP systems for food manufacturers include tracking production costs and quality during each stage of the manufacturing process, says Swedroe. “This can help pin-point areas that need to be targeted for process improvement to achieve cost reductions, higher quality and less scrap.”
For food retailers, having accurate point-of-sale information – along with tools to analyse this more readily available information – allows store managers to react more quickly to the need to modify operations and promotional efforts, Swedroe says. “For instance, a higher quality product with a relative long time to expiration date can be targeted to higher end points of sale and thereby command premium prices, [while] products of lower quality or that have a shorter time to expiration date can be targeted to lower end points of sales.”
Whether it is a food manufacturer or retailer, however, the arguably most important benefit that ERP systems can offer has to do with increasing food safety. Proper lot control and monitoring is imperative, for instance, says Swedroe, and with the techniques and tools an ERP system can provide, the sales of expired lots should not occur. “Safeguards include management notification/alerts to lots that are approaching their expiration dates – enabling management to proactively identify these lots and remove them from inventory – and linking the lot expiration date, and shipping information lead times to the destination address, so that shipments of lots that will expire before or shortly after they arrive at their destination can be prevented,” he says. If the product does happen to filter down to food retailers, says Swedroe, if the lot number is made a standard element required on product barcodes, the system can alert the cashier or consumer that the product being scanned has an expired lot.
“The impact of the ability to go from weeks to literally just a few clicks [in tracing a food safety breach] can mean someone’s life,” says Solarsoft marketing manager Diane Murray. “The ability to be able to minimise the impact can also be significant in terms of reduction of financial impact – it could mean the difference between paying a single lawsuit versus putting your company out of business.”