Suppliers of “on the cloud” ERP claim to offer a low-risk way of implementing the systems at a time of cost pressure and the need to enhance efficiency.
Similar to the majority of industries in today’s gloomy economy, the food sector is faced with the need to cut costs and improve efficiency, which ERP systems can help companies realise. However, the idea of implementing a brand new management system in an already delicate financial environment can make some companies wary, as choosing the wrong system could mean a huge loss in terms of investments, training time and a company’s bottom line.
“ERP systems are definitely an investment, and companies are currently stretched in our economy,” says Tom Pirko, president of US food and beverage consulting firm Bevmark LLC. However, he adds: “When times are hard is exactly when you should be making those investments to save yourself, instead of waiting. Competitively, you have no choice.”
So how are food manufacturers finding a balance between implementing ERP systems but in a relatively low-risk way?
In the past, food processors only had two options if they found their management systems were not up to par – either continue to live with the status quo, or make large investments in IT software. However, there are now many ERP system options available that use a low-cost cloud – or ‘software as a service’ (SaaS) – according to US-based Plex Online Systems. It claims to have a cloud computing platform that can deliver a complete solution for food manufacturers (i.e. production management, inventory management, quality management, financial management) via web browsers, with no hardware or software purchases.
With SaaS solution providers handling the maintenance and management of data off-premise, employees have the ability to access real-time data anytime from anywhere, as long as they have access to an Internet connection. This degree of accessibility is key for companies who have operations in more than one location, and – since the management and maintenance of the system is also outside the responsibility of the user – this means one less burden. “Food manufacturers are facing a choice – they can continue to manage increasingly complex processes, product genealogy, quality schemes, and daily production through paper record keeping or they can adopt a modern ERP system that facilitates electronic record keeping,” says a Plex Online Systems spokesperson.
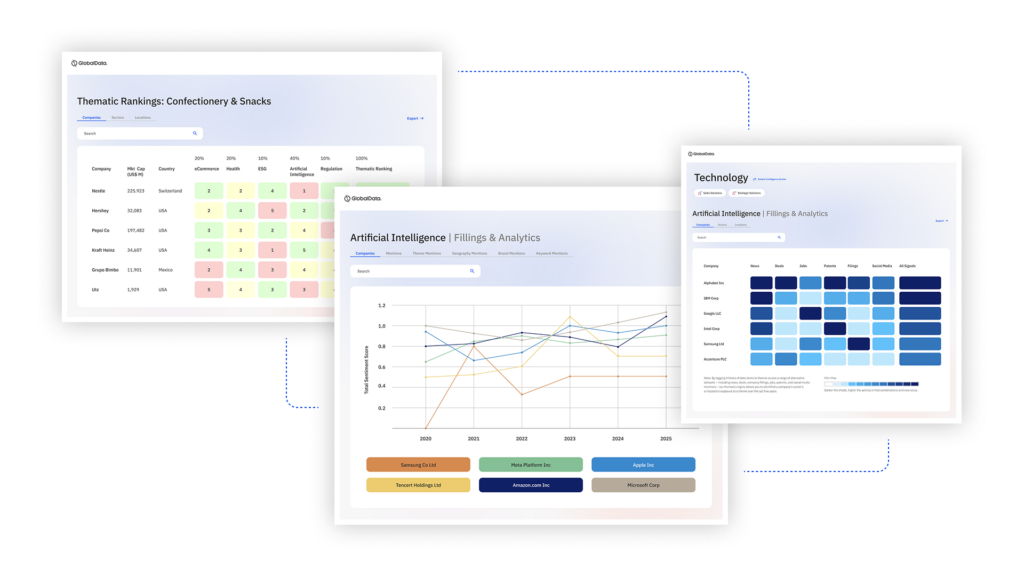
US Tariffs are shifting - will you react or anticipate?
Don’t let policy changes catch you off guard. Stay proactive with real-time data and expert analysis.
By GlobalDataJames Wise of Canadian-British ERP software company Solarsoft Business Systems acknowledges cloud solutions might be lower-cost alternatives to managing operations in-house with software. “[The food industry] is so regulated and data is your lifeblood as a company,” he says. However, he adds: “I think most companies want to keep that information under their own control [in-house].”
Wise contends that some cloud systems lack flexibility. “ERP systems for food and beverage industries need to be set up to handle individual customers’ needs, and [cloud service providers] don’t like that in the cloud environment…it ups their costs.”
According to American Internet-based business software suite company NetSuite, however, the cloud is actually a more flexible alternative to legacy ERP platforms. For instance, problems with on-premise customisations have to do with the burden of so-called “version-lock”. This occurs when a particular version of an ERP application has been customised so much, it is no longer practical to install a newer version of the application because customisations could be lost in the process. According to a 2010 Aberdeen Research report, two-thirds of completed ERP deployments are not running the latest release.
With cloud-based ERP on the other hand, companies can develop new functionality in a matter of weeks, and carry over all customisations seamlessly to the latest release of the application, according to Roman Bukary, GM of manufacturing/wholesale and distribution at NetSuite. His company, for example, automatically releases new versions of its software every six months, with all customisations automatically upgrading, too. “When purchasing an ERP system, [companies] don’t have to make the decision of buying something that needs to last for 20 years – they know that new features will be coming out that will continue to add value to their business,” Bukary says.
Cloud solutions are not only flexible, but they can be cost-efficient, too. “In the old days, people would allocate somewhere around 5% of revenue just on their ERP systems – never mind the specialised staff or lost productivity in terms of upgrading or maintaining that software,” Bukary says. “When the switch goes from on-premise to the cloud – where you leverage it as a service – expenses drop from 5% to a tenth of a percent.”
Cloud systems also offer smaller food companies the opportunity to compete with much larger organisations, Ranga Bodla, NetSuite’s director of industry marketing, says. “When we’re talking about smaller food manufacturers – those that employ anywhere between 10 and 500 people – these are not people that are especially savvy with technology; they’re savvy with food,” he says. With more traditional, on-premise ERP systems, says Bodla, it is usually necessary to have people in-house to manage security, and access to the system and servers – but not with the cloud system. The cloud is a viable solution on a large scale too, as the increase of mergers and acquisitions as of late has increased the need for flexible ERP customization in the food industry – with newly combined companies finding themselves with different sets of heterogeneous ERP solutions that need to talk to one another at the headquarters level and across multinational subsidiaries.
Finally, speed of deployment – and with it, speed of return – are also important benefits that cloud systems can boast versus an on-premise ERP. “ROI [return on investment] that a company is able to realise with a cloud system is typically measured in months, whereas, when you talk about traditional on premise systems, ROI is measured in years – because the implementations usually span multiple years,” says Bodla. “Once food companies are able to realise almost immediate value, they can then ease in other functionality over time.”