As yet another recall of tainted foods sweeps the US, the spotlight will surely focus on what the country’s regulators and policy makers must do to secure the safety of the nation’s food supply. Katy Humphries suggests that the industry and regulators alike must begin to rethink their damage limitation approach.
As the list of products affected by the recall of hydrolyzed vegetable protein (HVP) produced by Nevada-based ingredients firm Basic Food Flavors grows, US consumers will likely be asking themselves whether the processed foods purchased at grocery stores are safe.
A quick look at the statistics draws the conclusion “possibly not”…
True, the current nationwide recall has not, as yet, been linked to any illnesses. However, according to figures from the Centers for Disease Control and Prevention (CDC), each year 76m Americans fall sick because of food-borne illnesses.
To put this in context, the US population is a little over 300m people, so a staggering one in four US citizens report being sickened by the food they eat every year.
Around 5,000 Americans die of food borne illnesses each year.
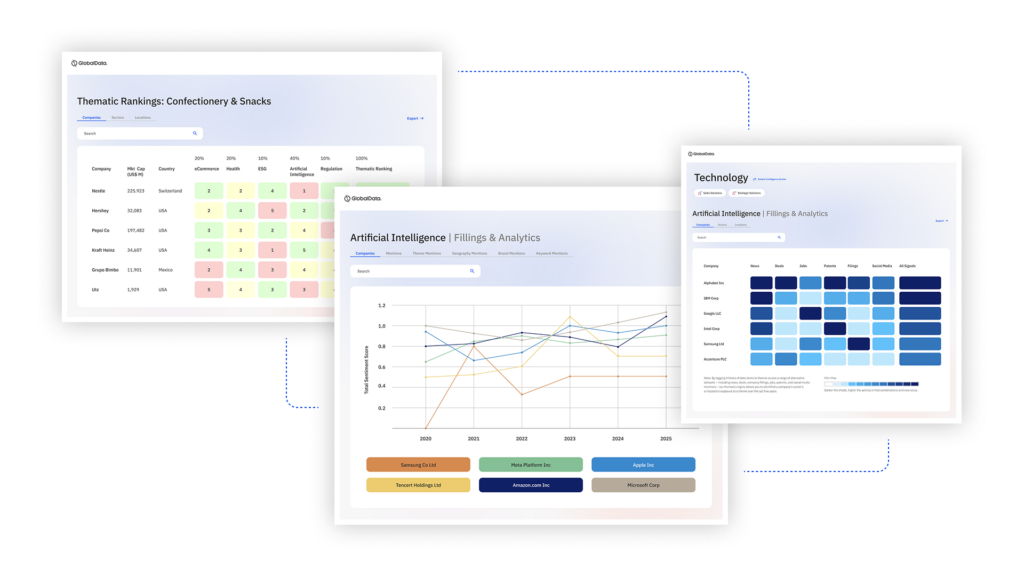
US Tariffs are shifting - will you react or anticipate?
Don’t let policy changes catch you off guard. Stay proactive with real-time data and expert analysis.
By GlobalDataIn some ways, the HVP recall is just another to add to an increasingly long list of high-profile food safety scares. Most recently it was salmonella in cookie dough; before that it was salmonella in peanut oil; then there was E.coli in beef products and salmonella in spinach.
These highly publicised recalls have all generated a lot of headlines and sound bites from safety regulators and policy makers. But have they resulted in any actual change?
There has certainly been a lot of bustle at the US Food and Drug Administration and US Department of Agriculture.
In recent months there has been much talk of improving traceability, the FDA has revised its Food Code and food industry fees have been introduced to provide regulators with some much needed funding.
The White House said it is taking “a new public health-focused approach to food safety”, basing its plan on three core principles – prioritising prevention, strengthening surveillance and enforcement, and improving response and recovery.
This line of thinking is also evident in the Food Safety Enhancement Act, which has passed the House of Representatives but still awaits approval from the Senate.
The act would provide the FDA with greater enforcement powers and resources to prevent the spread of food-borne illnesses.
And, indeed, the story of inaction and delay that marks this latest scare highlights the need for the Senate to boost the regulator’s powers.
Basic Food Flavors first learned of the presence of salmonella in its facility on 21 January when its private lab found salmonella in environmental samples collected at the site. The contamination was confirmed when two further tests came back positive.
Nevertheless, the FDA revealed last week that the company continued to ship HVP paste and powder to its food manufacturer customers until 15 February – almost a month after it was first alerted to the problem.
For its part, the FDA did not learn of the contamination until a customer of Basic Food Flavors discovered salmonella contamination in routine tests. The food standards watchdog launched an investigation on 12 February, when it too detected salmonella on production equipment.
A recall was not initiated until 26 February, three full weeks after the ingredients manufacturer began discussions with the FDA and six days after the FDA recommended a recall.
Once again, the FDA’s powerlessness to order a recall must be drawn into question.
The FDA also said that it found a number of issues at the company’s plant, which the company did little to correct in the interim between the discovery of salmonella contamination and the initiation of the recall.
Basic Food Flavors failed to adequately sanitise equipment and properly installed and maintained plumbing also hampered floor drainage, FDA inspectors claimed.
So, a manufacturing site that was clearly somewhat lacking combined with management that failed to act when first alerted to salmonella contamination has resulted in a recall that will surely be much larger than if the company had acted immediately to halt shipments and alert its customers to the issue.
It is impossible to say with any degree of certainty why Basic Food Flavors failed to act, although the incident does smack of an attitude of “damage limitation” that seems to reign supreme in US food safety.
Opponents to increased safety regulation regularly bemoan the supposed higher costs associated with additional red tape. But with food-borne illnesses costing the US economy US$152bn a year, the financial imperative to boost food safety in the country is undeniable.