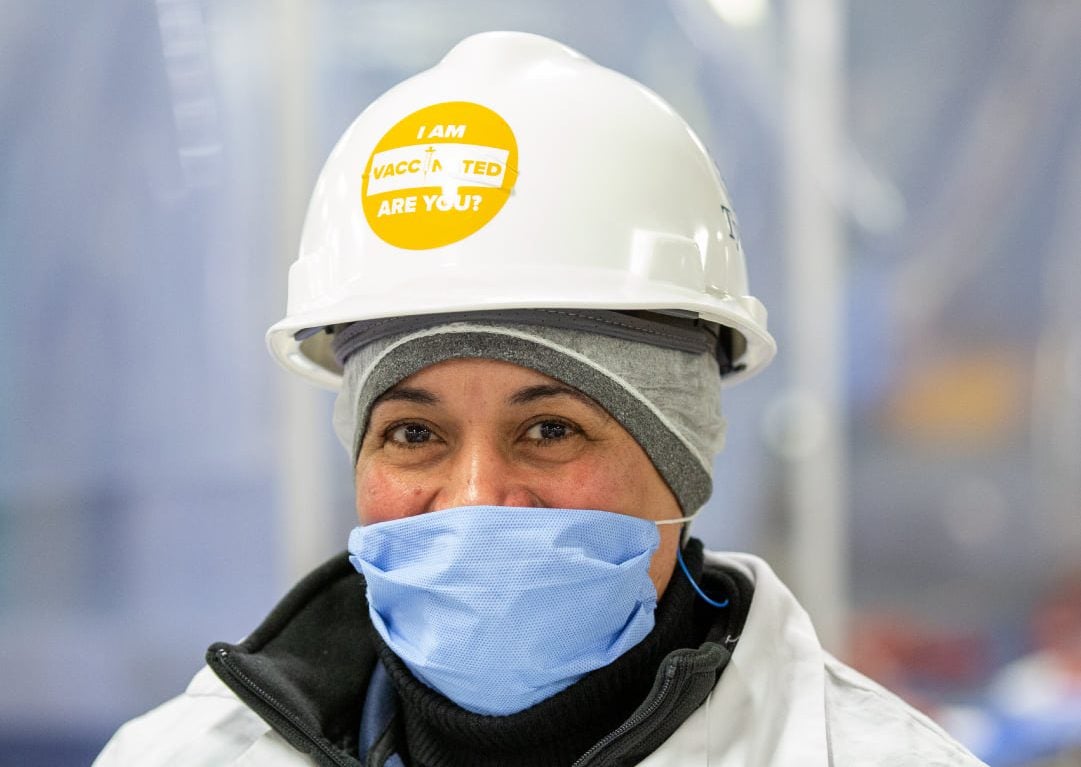
Tyson Foods plans to invest more than US$1bn in automation across its plants over the next three years to reduce “labour-intensive processes”.
The US$1.3bn that will be injected through to the end of the meat group’s fiscal 2024 year will “increase yields, reduce labour costs and associated risks, and ultimately deliver cumulative savings”, the company said in conjunction with its investor day presentation yesterday (9 December).
The move accompanies a productivity programme revealed in November to realise more than $1bn in “recurring savings” over the same time frame, with $250m expected from digital technologies such as artificial intelligence and “predictive analytics”.
Labour shortages have hit the entire US packaged food industry and other sectors. The current dearth of available workers has affected the ability of Tyson and other companies to meet consumer demand as the economy opens up from the worst of the pandemic notwithstanding the yet unknown implications from Omicron.
While Arkansas-based Tyson did not say the push to automation will come with job losses, the Jimmy Dean brand owner noted the labour required will be reduced by 3,150 across the group by 2024, in stages over the three years. Instead, the initiative will be geared toward “upskilling” workers, Tyson said.
President and CEO Donnie King added on a webcast presentation: “Today, across the organisation, we have open frontline roles, many of which are harder to fill. So we plan to use automation to reduce the number of hard-to-fill roles, and in doing so, we will help make life a little easier for our frontline team members.
“But headcount is just part of the story. Just as important, automation will help us increase volumes, improve reliability, and reduce cost over the mid- to long- term.”
The investment in automation was broken down into individual fiscal years along with a guide on the reduced labour need: $70m in 2021 (150 positions); $540m the following year (1,100); $340m in 2023 (900); and $400m in the final year of the programme (1,000).
King continued: “Staffing issues have been a significant challenge for us over the last two years. Labour availability has impacted our ability to service the customers the way that we’d like.
“We discovered that we don’t have to solve the nation’s labour issues. We have to solve those issues for Tyson and that’s what we began to do.
“It’s a very simple approach here: to take away the more difficult higher turnover jobs that we have and upskill the labour that we have and create greater value and better return on all of our investment dollars, not only for the technology, but from those team members as well.”
Meanwhile, Tyson expects to outperform the meat market with volumes anticipated to grow by an annual compound growth rate of 2% versus 1% for animal proteins overall. The objective will be supported by the opening of 12 new plants over the next two years to add 1.3 billion pounds of capacity. Added-value products will make up 50% of volumes by 2024.
Alternative proteins will also play a part, with Tyson present in the market through its Raised and Rooted brand.
Noelle O’Mara, the president for the prepared foods division, said: “Tyson will continue to drive growth in alternative proteins by expanding our portfolio both through Raised and Rooted and our power brands. And by further developing our global footprint, these expansions will be built on the core capabilities and infrastructure that we have built across procurement, R&D, manufacturing and supply chain.”
GlobalData research: Filings buzz: tracking industrial automation in food manufacturing